For thirty years they have trusted us
for their flow simulation projects
Small companies and large international groups, consultants and teachers, many have used ExtendSim simulation models to understand and improve their organization, because the software’s first quality is its adaptability to all types of fields and issues.
Airbus, Air France, Alcan RioTinto, Areva, Arkema, AstraZeneca, Aventis, BioMérieux, Bouygues, CTIF, CERN, Collins, Constellium, Cristal, Dade Behring, Danone, Dekra, ELI Lilly, Elkem, Estavayer Lait, Eurenco, Eurocast, Fenwick Linde, Finaref, Firmenich, Frontex, GlaxoSmithKline, Hager Electro, Hitachi, Ifremer, Jacobs, Johnson&Johnson, Kelloggs, Kerneos, La Poste, Lafarge, MEDA, Mobalpa, Monsanto, Norpac, Novatech, OCP Maroc, Pepsico, Procter&Gamble, Quick Restaurants, Rhodia Solvay, Sagem, Seqens, SNCF, Sofraden, Technip, ThyssenKrupp, Total, Toyota, Trivium Packaging West France, Unilever, Vico, Yoplait.
CERN – CRSSA – Ecole des Mines d’Albi – Ecole des Mines de Nancy – Ecole d’Ingénieurs du Valais – Ecole d’Ingénieurs et d’Architectes de Fribourg –Ecole Polytechnique Fédérale de Lausanne – Ecole Royale Militaire de Bruxelles – ENSAM – ENTPE – ESCI de l’Ain – Escola Superior Tecnologia Gestão da Guarda – ESIEE – ESLI Redon – ESSEC – Isara Lyon – INRA – INSA Rouen – Hochschule für angewandte Wissenschaften Augsburg – WHU Otto Beisheim School of Management – Otto-von-Guericke Universität Magdeburg – IUT de Béthune, de Chalon, du Havre, de Lorient, de Mulhouse, de Vesoul – INSEAD – Technische Universität Clausthal Technische – Universität München – Université Lyon II – Université Paris I – Université de Chypre, Dublin, Duisbourg, Gênes, Liège, Plymouth, Patras, Rome, Thessalonique…
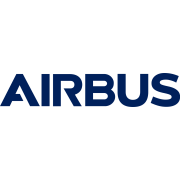
In Toulouse, Saint-Nazaire, Nantes, Germany and Spain, we built models for multiple production lines, and trained engineers in simulation. The processes are sometimes very specific (chemical machining, assembly of large parts, rare tools), the issues remain those of any manufacturer: task splitting, schedules and operator skills, optimization of tool changes, validation of scheduling.
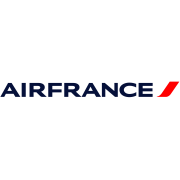
Air France has been using ExtendSim simulation models since 2008 to improve the rate of successful connections in Terminal 2 of Roissy-Charles-De-Gaulle airport. The simulation model is used each season on new flight plans, adjusting traffic flows, the number of shuttles, etc. to current situations.
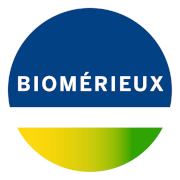
After a model in 2011 about analysing laboratory capacity, a BioMérieux team was trained in ExtendSim and the dynamics of conveyor systems, becoming the privileged interlocutor for the construction of models on the cycles of use and decontamination of incubators (2012-2013). The basic model has been adapted to other sites, thus becoming more generic (2015).
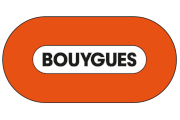
Several Bouygues divisions and sites have used simulation to validate the safety and capacity of large sites open to the public. Flows of users are mixed with flows of employees, professionals and often vehicles. Scenarios include extreme conditions (rush hour, special events), elevator logics and secure access.
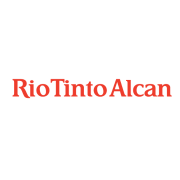
As soon as ExtendSim was distributed in France, the Voreppe Research Center, which works for all of the group’s factories, chose the software to study and improve the performance of production lines for products made from alumina. The electrolysis plants then used flow simulation independently, and 1Point2 developed a specific library of blocks suitable for metal flows.
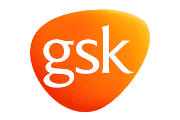
For more than 10 years, 1Point2 has been working regularly on models of drug packaging lines, for which generic tools have been developed, making it possible to test the rates (bottles per minute), the stocks of consumables to be refilled, the types of internal shutdowns of the line, the intervention positions of the operators, the links with the automation and the logic of the upstream/downstream sensors on the conveyors, the related movement of the pallet flows.
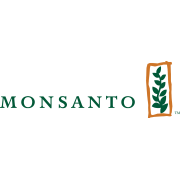
Flow simulation models have been built to optimize the distribution of tasks and resources for the corn crop cycle, from sowing to drying and conditioning of the mature product, taking into account several fields with their weather conditions and specific logistics. A multiplicity of parameters for a puzzle that only simulation could overcome…
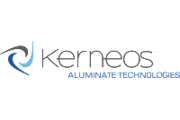
For this expert company in special cements, 1Point2 described the production lines of several sites, from the initial grinding to the consumption of the packaged products. The simulation made it possible to modulate the product campaigns according to favorable EDF time slots, to adapt the throughputs of the crushers, the use of silos and packaging, and ultimately to guarantee better compliance with manufacturing deadlines.
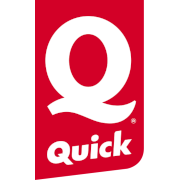
It all started with the study of the impact of the “drive” on the surrounding roads, for several restaurant sites. Then the flow simulation gained the planning of the team members, the configuration of the workstations, the production ranges, the quality of the service, showing the potential gains by the reduction of waste, the better usage of the equipment, the energy savings, the finest adequacy of the teams to the needs.
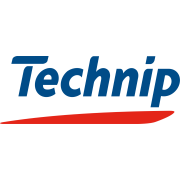
Due to its profession, Technip encounters very complex systems, often with large-scale issues. Flow simulation must support the engineering force on these projects, and ExtendSim has been used to validate layouts, test warehouses, size dynamic storage areas, optimize port logistics flows.